Addressing Challenges In Automated Visual Inspection Of Lyophilized Vials
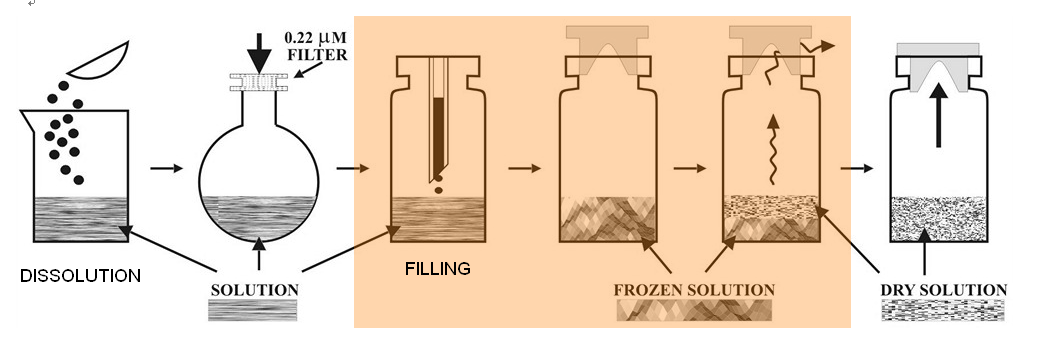
Table of Contents
The importance of visual inspection in pharmaceutical quality control is paramount. It's a critical step in ensuring that each vial meets stringent quality standards before reaching patients. While manual inspection has traditionally been the norm, the increasing demand for higher throughput and reduced human error is driving the adoption of automated visual inspection systems. However, the inherent complexities of lyophilized vials pose significant hurdles for automation. Lyophilization itself introduces variations in the final product, making automated defect detection a complex undertaking.
Challenges Related to Lyophilized Vial Characteristics
The physical characteristics of lyophilized vials present several challenges for automated visual inspection systems.
Variability in Lyophilized Cake Appearance
The lyophilized cake, the dried drug product within the vial, exhibits inherent variability in its appearance. This variability stems from the lyophilization process itself, which can result in variations in:
- Cracks and Fissures: The formation of cracks or fissures in the lyophilized cake is common and can be difficult to distinguish from more serious defects.
- Cake Collapse: Partial or complete collapse of the lyophilized cake can indicate problems with the lyophilization process or product instability.
- Porosity and Texture: Variations in the porosity and texture of the cake can affect its appearance and complicate automated detection.
Differentiating between acceptable variations and unacceptable defects requires sophisticated algorithms capable of analyzing subtle differences in cake structure and appearance. Different lyophilization cycles, even with the same formulation, can lead to variations in the final cake appearance, making consistent automated detection a significant challenge.
Subtle Defects and Low Contrast
Detecting subtle defects in lyophilized vials is another significant hurdle. These defects often present with low contrast against the vial background, making them difficult to identify even for trained human inspectors. Examples of such subtle defects include:
- Small Particles: Microscopic particles in the lyophilized cake or on the vial walls can be challenging to detect.
- Discoloration: Subtle changes in color or shade can indicate product degradation or contamination.
- Surface Imperfections: Minor scratches or blemishes on the vial surface can interfere with image analysis.
Effective detection requires advanced image processing techniques and highly sensitive lighting systems to enhance contrast and highlight these subtle imperfections. Current technologies struggle with consistently detecting these defects due to limitations in resolution, sensitivity, and algorithm sophistication.
Impact of Vial Material and Manufacturing Variations
The material and manufacturing process of the vials themselves can also influence the accuracy of automated visual inspection. Variations in:
- Glass Clarity and Thickness: Inconsistent glass clarity or thickness can lead to variations in light refraction and reflection, impacting image quality.
- Reflections and Refractions: Light reflections and refractions from the vial's surface can obscure the lyophilized cake, making defect detection difficult.
- Vial Geometry: Slight variations in vial geometry can also affect image analysis and the performance of automated inspection systems.
These variations necessitate the development of robust algorithms that can compensate for these inconsistencies and maintain accuracy despite varying vial characteristics. Algorithm development must account for these variables to provide reliable results.
Technological Challenges in Automated Visual Inspection
Beyond the inherent challenges of lyophilized vials, technological limitations further complicate automated visual inspection.
Algorithm Development and Optimization
Developing robust algorithms for accurate defect identification and classification in lyophilized vials is a significant challenge. This involves:
- AI/ML Model Training: Training artificial intelligence (AI) and machine learning (ML) models requires vast amounts of high-quality training data representing a wide range of vial characteristics and defects.
- Handling Variations: Algorithms must be able to handle variations in lighting, vial characteristics, and lyophilized cake appearance without compromising accuracy.
- Defect Classification: Accurate classification of defects requires sophisticated algorithms capable of distinguishing between acceptable variations and unacceptable defects.
The complexity of the task necessitates continuous refinement and optimization of algorithms to improve detection accuracy and minimize false positives and negatives.
Hardware Limitations
Current imaging technologies also present limitations:
- Resolution Limitations: Achieving sufficient resolution to detect subtle defects requires high-resolution cameras and sophisticated imaging systems.
- Lighting Uniformity: Consistent and uniform lighting is crucial for accurate image acquisition. Specialized illumination techniques may be required to minimize shadows and reflections.
- Camera Technology: The choice of camera technology (e.g., CCD, CMOS) significantly impacts image quality and detection accuracy. Specialized cameras may be required for optimal performance.
Data Management and Analysis
Automated visual inspection systems generate massive amounts of data, requiring robust data management and analysis capabilities:
- Data Storage and Retrieval: Efficient storage and retrieval of large datasets are essential for efficient analysis and reporting.
- Data Analysis Techniques: Advanced data analysis techniques are needed to identify trends, patterns, and anomalies in the inspection data.
- Integration with QC Systems: Integration with existing quality control (QC) systems is vital for seamless data flow and traceability.
Ensuring data integrity and traceability throughout the entire process is crucial for maintaining compliance with regulatory requirements.
Conclusion
Automated visual inspection of lyophilized vials presents significant challenges, including the inherent variability in lyophilized cake appearance, the difficulty in detecting subtle defects, technological limitations in imaging and algorithm development, and the complexities of data management. Addressing these challenges is crucial for ensuring the quality and safety of lyophilized drug products. Continued research and development in advanced imaging techniques, improved algorithms, and robust data management systems are necessary to overcome these hurdles. This will lead to more efficient and reliable quality control processes and ultimately enhance patient safety. Explore further resources and solutions to optimize your automated visual inspection systems for lyophilized vials and ensure the highest standards of quality control are met in your manufacturing process. Investing in advanced Automated Lyophilized Vial Inspection solutions is an investment in patient safety and product quality.
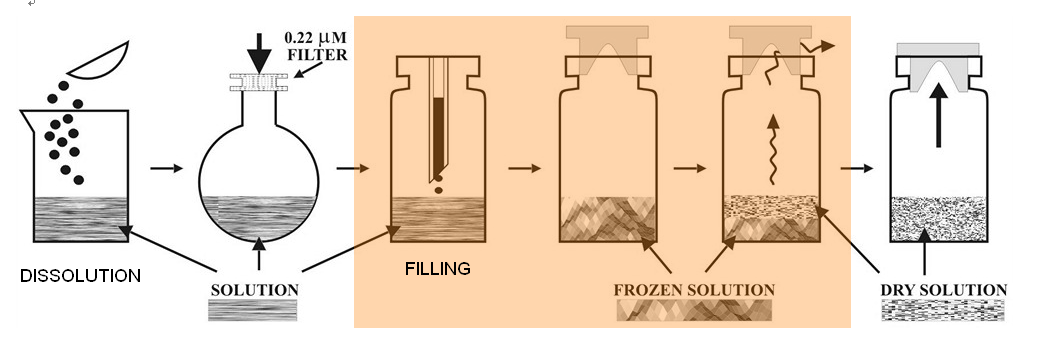
Featured Posts
-
Planifier Son Budget La Cle Pour Realiser Des Economies
May 11, 2025 -
Mueller Confirme Son Depart Du Bayern Munich Apres 25 Saisons
May 11, 2025 -
Ras Baraka Arrested During Protest Outside Newark Ice Detention Center
May 11, 2025 -
Uruguay La Historia Detras Del Nombre Semana De Turismo Y Su Significado Cultural
May 11, 2025 -
Marvels Henry Cavill Project Was Cancellation A Blessing In Disguise
May 11, 2025