Best Practices For Automated Visual Inspection Of Lyophilized Vials
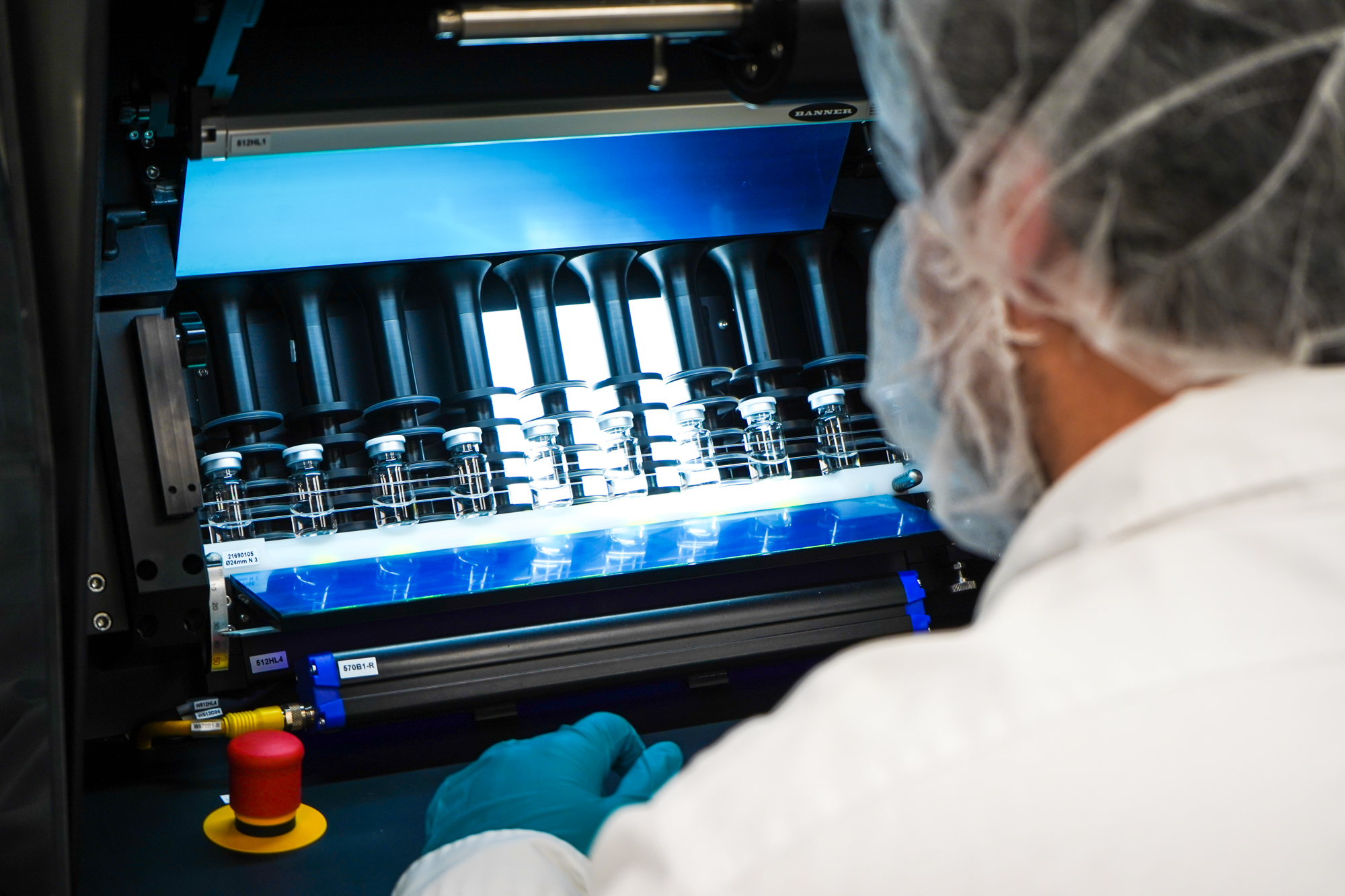
Table of Contents
Selecting the Right Automated Visual Inspection System for Lyophilized Vials
Choosing the right automated visual inspection system is the cornerstone of a successful implementation. The system must be capable of detecting subtle defects common in lyophilized vials while seamlessly integrating with your existing manufacturing workflow.
Key Features to Consider:
- High-resolution imaging: The system needs to capture incredibly detailed images to detect minute cracks, particulate matter, or discoloration in the lyophilized product and vial. Consider megapixel count and the clarity of images under various lighting conditions.
- Advanced algorithms: Sophisticated algorithms are crucial for reliably identifying a wide range of defects. These algorithms should be adaptable and capable of being trained on your specific product characteristics to minimize false positives and negatives. Look for systems that can differentiate between critical and non-critical defects.
- Adaptability and Flexibility: The system must be adaptable to handle various vial sizes, shapes, and formats to accommodate current and future product needs. Consider the ease of changeover between different vial types.
- Seamless Integration: Ensure the system can easily integrate with your existing production line, minimizing disruption and maximizing efficiency. Look for systems with robust data transfer capabilities and compatibility with your existing manufacturing execution system (MES).
- Robustness and Reliability: The system must be robust enough to withstand the rigors of a continuous production environment and deliver consistent performance with minimal downtime. Consider factors like mean time between failures (MTBF) and mean time to repair (MTTR).
- Data Management and Reporting: Comprehensive data management is essential for compliance with regulatory requirements (e.g., 21 CFR Part 11). The system should provide detailed audit trails, data logging, and reporting capabilities to facilitate quality control and regulatory inspections.
Types of AVI Systems:
Several technologies power AVI systems, each with strengths and weaknesses. Machine vision systems utilize cameras and sophisticated image processing algorithms to detect defects, while image analysis systems may incorporate additional techniques such as spectroscopy. Consider in-line systems, which integrate directly into the production line, or offline systems which inspect vials after lyophilization. Several leading manufacturers provide specialized solutions for lyophilized vial inspection, each offering unique features and capabilities. Researching different vendors and comparing their offerings is essential.
System Validation and Qualification:
Thorough validation and qualification are mandatory to ensure the system's accuracy and reliability. This process typically involves:
- Compliance with standards: The validation process must adhere to industry standards such as 21 CFR Part 11, ensuring data integrity and compliance.
- Qualification stages: This includes Installation Qualification (IQ), Operational Qualification (OQ), and Performance Qualification (PQ) to verify the system's correct installation, proper operation, and ability to meet pre-defined performance criteria.
- Comprehensive documentation: Meticulous documentation of every step of the validation and qualification process is crucial for regulatory compliance and future audits.
Optimizing the Automated Visual Inspection Process for Lyophilized Vials
Optimizing the inspection process ensures the system performs at peak efficiency and accuracy.
Lighting and Image Acquisition:
Proper lighting is crucial for high-quality image capture.
- Minimize shadows and reflections: Employ appropriate lighting techniques (e.g., diffused lighting) to eliminate shadows and reflections that can obscure defects.
- Optimal camera settings: Adjust camera settings (e.g., exposure, gain, focus) to optimize image clarity and contrast.
- Regular calibration: Regular calibration ensures consistent image quality over time, maintaining the accuracy of defect detection.
Defect Detection Algorithms:
The system's algorithms are key to identifying defects.
- Customization: Customize algorithms to target specific defects frequently encountered in lyophilized vials (e.g., cracks in the vial, particulate matter in the product, variations in fill volume).
- Regular updates: Regularly update and refine algorithms based on experience and evolving quality standards to maintain accuracy and minimize false positives/negatives.
- False positive/negative analysis: Continuously analyze the false positive and false negative rates and implement mitigation strategies to improve the system’s performance.
Data Analysis and Reporting:
Effective data management is crucial for compliance and process improvement.
- Data storage and retrieval: Implement a robust system for storing and retrieving inspection data, complying with all regulatory requirements.
- Comprehensive reports: Generate detailed reports for quality control purposes, providing insights into defect rates, trends, and potential process improvements.
- Predictive maintenance: Utilize data analytics to predict potential maintenance needs, minimizing downtime and ensuring consistent system performance.
Maintaining and Troubleshooting Automated Visual Inspection Systems
Preventative maintenance and effective troubleshooting are essential to maximize the system's lifespan and performance.
Preventative Maintenance:
- Regular cleaning and calibration: Follow a regular schedule for cleaning and recalibrating the system to maintain its accuracy and reliability.
- Preventative maintenance schedule: Establish a preventative maintenance schedule based on manufacturer recommendations and usage patterns.
- Spare parts inventory: Maintain an inventory of spare parts to minimize downtime during repairs.
Troubleshooting Common Issues:
- Identify and resolve errors: Develop procedures for identifying and resolving common system errors quickly and efficiently.
- Diagnostic tools: Utilize diagnostic tools and logs to pinpoint the source of problems.
- Timely repairs: Ensure timely repairs and maintenance to minimize downtime and maintain production efficiency.
Operator Training:
- Comprehensive training: Provide operators with comprehensive training on system operation, maintenance, and troubleshooting.
- Ongoing training: Offer ongoing training and updates to keep operators informed about system improvements and best practices.
Conclusion: Achieving Superior Quality through Automated Visual Inspection of Lyophilized Vials
Implementing automated visual inspection systems for lyophilized vials offers significant benefits in terms of improved product quality, increased efficiency, and enhanced regulatory compliance. Selecting the right system, optimizing the inspection process, and performing regular maintenance are all crucial steps. By following the best practices outlined in this article, pharmaceutical manufacturers can significantly enhance their quality control processes and ensure the delivery of safe and effective lyophilized products. Optimize your lyophilized vial inspection today! Improve your pharmaceutical quality control with advanced automated visual inspection.
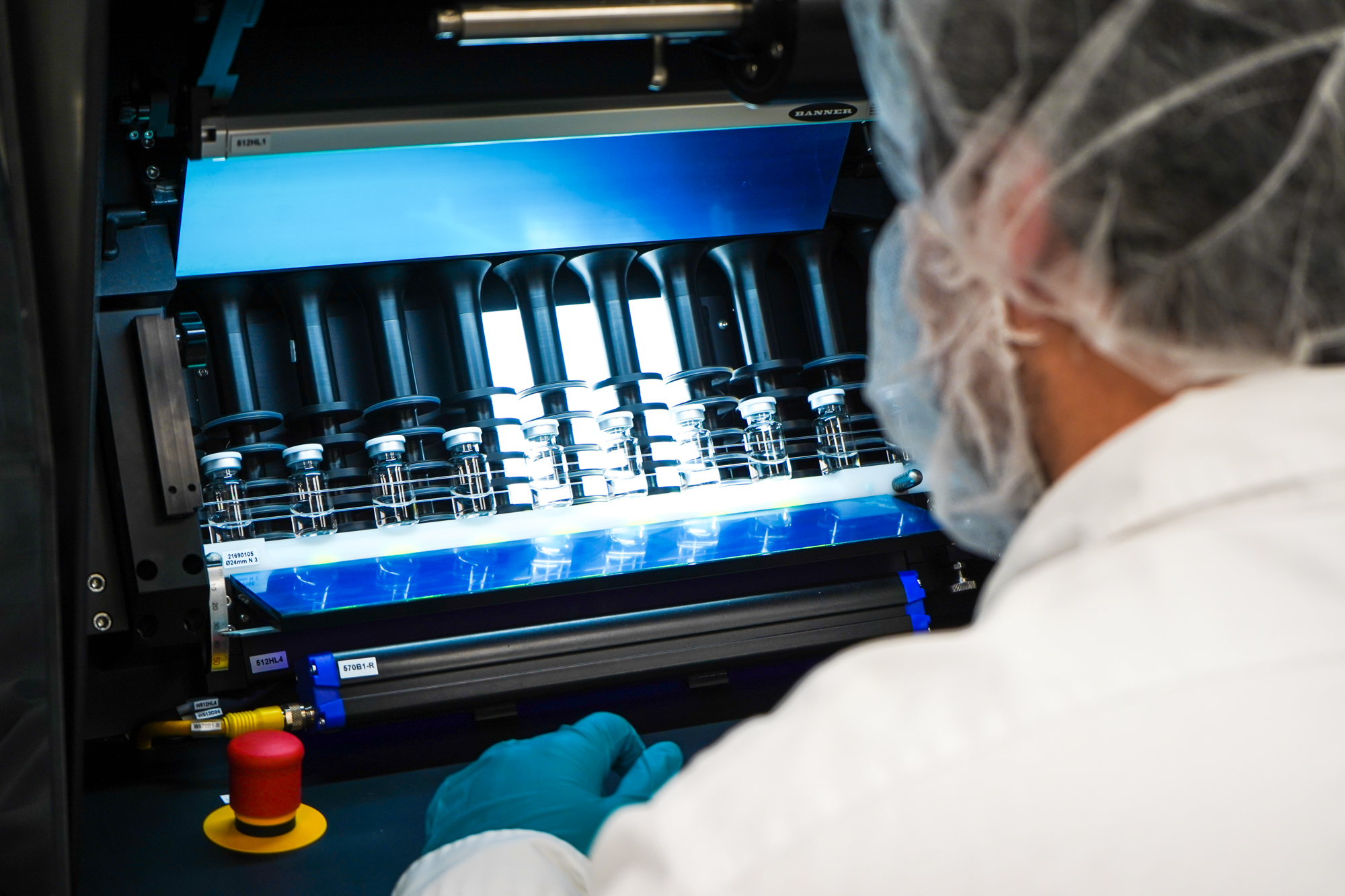
Featured Posts
-
L Avis D Un Animateur Veteran Sur L Arrivee De Hanouna A M6
May 11, 2025 -
Continued Heightened Border Security In The Netherlands A Response To Shifting Trends
May 11, 2025 -
Stellantis Ceo Decision Imminent American Executive A Leading Candidate
May 11, 2025 -
Amazon Boss Jeff Bezos James Bond Poll The Results Are In
May 11, 2025 -
Yankee Jazz Chisholms Early Season Stats Outperforming Aaron Judge
May 11, 2025