Challenges And Advancements In Automated Visual Inspection Of Lyophilized Drug Products
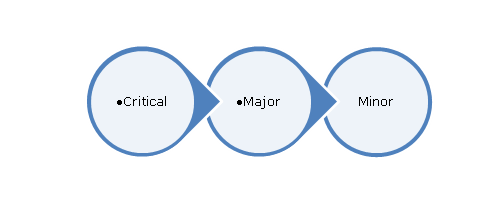
Table of Contents
Challenges in Automated Visual Inspection of Lyophilized Drug Products
Automated visual inspection of lyophilized drug products presents unique challenges due to the inherent complexities of the freeze-drying process and the subtle nature of potential defects.
Variability in Lyophilized Product Appearance
The freeze-drying process itself introduces significant variability in the final product's appearance. This makes consistent, reliable automated defect detection difficult.
- Variations in cake appearance: Cracks, fissures, and collapse are common variations, making it hard to define clear defect thresholds.
- Inconsistencies in color: Subtle shifts in color can be indicative of processing issues, but distinguishing them from natural variations is challenging.
- Presence of particulate matter: Small particles within or on the lyophilized cake can indicate contamination, necessitating high-resolution imaging for detection.
- Difficulties in standardized defect definition: Establishing universally accepted criteria for what constitutes a critical defect versus an acceptable variation remains a challenge.
This inherent variability necessitates sophisticated algorithms capable of distinguishing between acceptable variations and actual defects, a complex task requiring advanced image processing techniques.
Complex Image Analysis Requirements
Analyzing images of lyophilized drug products requires powerful image processing techniques to reliably detect defects.
- Need for high-resolution imaging: Subtle cracks, fissures, or small particulate matter often require extremely high-resolution imaging to be accurately identified.
- Advanced algorithms to differentiate between acceptable variations and critical defects: Sophisticated algorithms are crucial to filter out acceptable variations and focus only on defects that could compromise product quality and patient safety.
- Handling variations in lighting and background conditions: Consistent lighting and background control is crucial for reliable image analysis; changes in these parameters can significantly affect the accuracy of defect detection.
The complex nature of these requirements emphasizes the need for continuous improvement in image processing capabilities.
Cost and Implementation Barriers
Implementing AVI systems for lyophilized drug products can present considerable financial and logistical hurdles.
- High initial investment costs for AVI systems: State-of-the-art AVI systems represent a significant capital investment for pharmaceutical manufacturers.
- Need for specialized expertise for system integration and maintenance: Successful integration and maintenance require specialized personnel with expertise in both pharmaceutical manufacturing and automated inspection systems.
- Validation requirements for regulatory compliance: Thorough validation is essential to demonstrate the accuracy and reliability of the system, adding to the time and cost involved in implementation.
These substantial barriers can deter smaller companies from adopting AVI technologies, highlighting the need for more cost-effective and user-friendly solutions.
Advancements in Automated Visual Inspection Technologies
Despite the challenges, significant advancements in technology are driving improvements in AVI systems for lyophilized drug products.
Advanced Image Processing Algorithms
The application of artificial intelligence (AI) and machine learning (ML) is revolutionizing AVI.
- Machine learning (ML), artificial intelligence (AI), deep learning applications for improved defect detection accuracy: These algorithms learn from large datasets of images, improving their ability to identify subtle defects with increasing accuracy over time.
- Automated training and model refinement: Automated training processes minimize the need for manual intervention, enhancing efficiency and reducing human error.
These algorithms offer superior pattern recognition and anomaly detection compared to traditional methods, leading to more accurate and consistent defect detection.
High-Resolution Imaging Techniques
New imaging technologies provide significantly improved image quality.
- Improved camera sensors and lighting systems: Advances in sensor technology and lighting design enable the capture of higher-resolution images with improved contrast and clarity.
- Multi-spectral imaging: Capturing images across multiple wavelengths allows for the detection of defects invisible to the naked eye or standard imaging techniques.
- 3D imaging capabilities for enhanced defect visualization: Three-dimensional imaging provides a more complete picture of the product, allowing for better defect characterization and identification.
These advancements are enabling the detection of increasingly subtle defects, improving the overall accuracy of AVI systems.
Improved System Integration and Data Management
Modern AVI systems are designed for seamless integration within the existing manufacturing infrastructure.
- Seamless integration with existing manufacturing systems: This allows for real-time data acquisition and integration with other quality control systems.
- Real-time data analysis and reporting: Immediate feedback on defect rates and trends allows for proactive adjustments to manufacturing processes.
- Automated quality control documentation: Automated documentation streamlines regulatory compliance and reduces the risk of errors.
These improvements significantly enhance efficiency, data traceability, and compliance with regulatory requirements.
Conclusion
Automated visual inspection is a vital tool for maintaining the high quality and safety standards demanded for lyophilized drug products. While challenges remain regarding the inherent variability of these products and the complexity of image analysis, rapid advancements in imaging technologies, AI, and machine learning are driving significant improvements in AVI systems. These advancements result in increased accuracy, enhanced efficiency, and long-term cost reductions. Embrace the future of pharmaceutical quality control by exploring the latest advancements in automated visual inspection of lyophilized drug products. Investing in robust AVI systems is essential for ensuring the safety and efficacy of your freeze-dried medications, optimizing your manufacturing processes, and meeting stringent regulatory requirements. Learn more about the benefits of implementing cutting-edge Automated Visual Inspection technologies today!
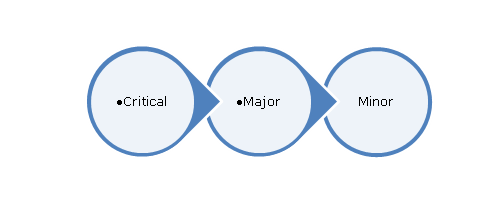
Featured Posts
-
Remembering Chris Newsom Halls Crossroads Baseball Tournament Kicks Off
May 12, 2025 -
Judges Dominant Start Highlights Braves Early Season Struggles
May 12, 2025 -
Major League Baseball Suspends Jurickson Profar For 80 Games Due To Ped Use
May 12, 2025 -
Fans Catch A Peek Selena Gomez And Benny Blancos Unexpectedly Intimate Moment
May 12, 2025 -
Razgovor Putina I Dzhonsona Aktsent Na Rossiyskikh Atomnykh Podlodkakh
May 12, 2025
Latest Posts
-
The Most Emotional Rocky Movie According To Sylvester Stallone
May 12, 2025 -
Which Rocky Movie Touches Sylvester Stallone The Most
May 12, 2025 -
Stallone Reveals His Top Rocky Movie A Touching Choice
May 12, 2025 -
Sylvester Stallone Picks His Most Emotional Rocky Film
May 12, 2025 -
Sylvester Stallones Favorite Rocky Movie The Franchises Most Emotional Entry
May 12, 2025