Enhanced Automated Visual Inspection For Lyophilized Vials: Strategies For Success
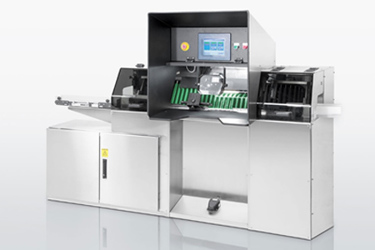
Table of Contents
H2: Selecting the Right Automated Visual Inspection System
Choosing the optimal automated visual inspection system is crucial for achieving successful implementation. The selection process must carefully consider various factors related to the specific needs and challenges posed by lyophilized vials.
H3: Understanding Different Inspection Technologies
Several technologies are available for automated visual inspection, each with unique capabilities. These include:
- Machine Vision Systems: These systems utilize cameras and sophisticated algorithms to analyze images of the vials, identifying defects like cracks, particulate matter, and fill level discrepancies. They are cost-effective and widely used for basic inspection needs.
- AI-Powered Systems: Artificial intelligence (AI) and deep learning algorithms are increasingly incorporated into automated systems. These systems can learn and adapt to detect even subtle defects that might be missed by traditional machine vision, offering enhanced accuracy and adaptability. They are particularly effective in identifying complex defects and variations.
- 3D Imaging Systems: Unlike 2D systems, 3D imaging provides a complete three-dimensional representation of the vial, enabling the detection of defects that may not be visible in 2D images, such as vial collapse or irregularities in the stopper.
Bullet Points:
- 2D vs. 3D Imaging: While 2D imaging offers speed and cost-effectiveness, 3D imaging provides superior defect detection capabilities for complex issues. The choice depends on the specific needs and critical quality attributes.
- Lyophilized Vial Specifics: Lyophilized vials present unique challenges, including potential for cracks in the vial or stopper, cake collapse, and the presence of particulate matter within the vial. The chosen system must be capable of detecting these specific defects effectively.
- Throughput, Integration, and Compliance: System selection must consider the required throughput to keep up with production demands, seamless integration with existing manufacturing lines (including upstream and downstream processes), and full compliance with relevant regulatory guidelines like GMP (Good Manufacturing Practices) and 21 CFR Part 11.
H2: Optimizing the Inspection Process for Lyophilized Vials
Even the most advanced automated visual inspection system requires careful optimization to deliver accurate and reliable results for lyophilized vials.
H3: Pre-Inspection Preparation and Handling
Proper handling and preparation are critical for successful automated visual inspection.
Bullet Points:
- Vial Orientation and Presentation: Consistent vial orientation and presentation are crucial for ensuring consistent illumination and minimizing shadows, leading to improved image clarity and accuracy. Automated systems often include mechanisms to control vial orientation.
- Minimizing Background Noise: Controlling lighting conditions and minimizing vibrations are essential to reduce background noise and improve image clarity. Dedicated lighting systems and vibration-dampening equipment are crucial.
- Standardized Operating Procedures (SOPs): Establishing and adhering to detailed SOPs for vial handling, system operation, and data interpretation ensures consistent results and regulatory compliance.
H2: Data Analysis and Reporting for Enhanced Quality Control
Modern automated visual inspection systems generate vast amounts of data, and effective analysis is key to maximizing their value.
H3: Utilizing Advanced Data Analytics
Data analytics plays a vital role in enhancing quality control and process optimization.
Bullet Points:
- Integration with QMS: Integrating the automated inspection system with a quality management system (QMS) allows for efficient data management, trend analysis, and reporting.
- Comprehensive Reports and Traceability: Generating comprehensive reports with detailed information on detected defects and their location is crucial for regulatory compliance and root cause analysis. Complete traceability is essential.
- Statistical Process Control (SPC): Implementing SPC techniques allows for real-time monitoring of process parameters and identification of potential deviations, enabling proactive intervention and defect prevention.
H2: Addressing Challenges and Ensuring Seamless Integration
Implementing automated visual inspection systems requires careful planning and execution to overcome potential hurdles.
H3: Overcoming Integration Hurdles
Successful integration requires addressing several potential challenges.
Bullet Points:
- Validation: Rigorous validation procedures are necessary to ensure the system’s accuracy, reliability, and compliance with regulatory requirements. This involves qualification and verification tests.
- Operator Training: Proper training for operators and maintenance personnel is essential to maximize system uptime and minimize errors.
- Minimizing Downtime: Strategies for preventative maintenance and prompt troubleshooting are crucial for minimizing downtime and maximizing the return on investment.
3. Conclusion:
Implementing enhanced automated visual inspection for lyophilized vials offers numerous advantages. From improved quality control and increased efficiency to enhanced regulatory compliance, the benefits are significant. By carefully selecting the right system, optimizing the inspection process, effectively analyzing the generated data, and addressing potential integration challenges, pharmaceutical manufacturers can drastically improve their lyophilized vial production. Don't let manual inspection limitations hinder your success. Explore the possibilities of advanced automated visual inspection in lyophilization and improved automated visual inspection for lyophilized products today. Contact us to learn more about our solutions and how we can help you achieve optimal quality and efficiency in your lyophilization process.
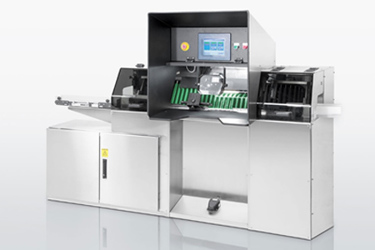
Featured Posts
-
Medieval Book Cover Illustration Merlin And King Arthurs Untold Story
May 11, 2025 -
I Fonitiki Ygeia Tis Tzesika Simpson Istories Kai Fimes
May 11, 2025 -
Boston Celtics Clinch Division After Blowout Victory
May 11, 2025 -
The China Factor How Market Dynamics Affect Bmw Porsche And Other Automakers
May 11, 2025 -
New Mom Lily Collins Models For Calvin Klein Images From The Campaign
May 11, 2025