Overcoming Hurdles In Automated Visual Inspection Of Lyophilized Vials
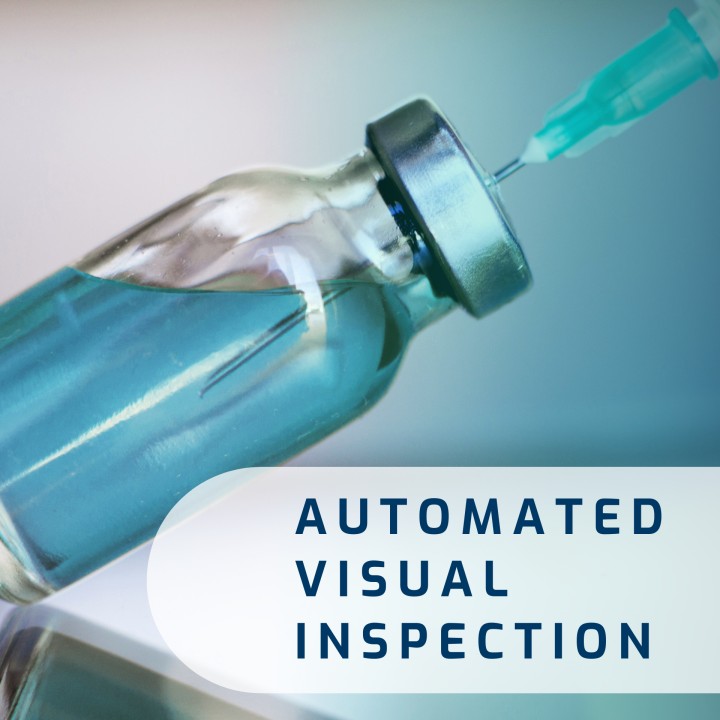
Table of Contents
Challenges in Image Acquisition for Lyophilized Vials
The inherent characteristics of lyophilized vials create significant difficulties in acquiring high-quality images suitable for accurate automated visual inspection. These challenges stem from variations in the lyophilization process itself and the physical properties of the vials and their contents.
Variations in Lyophilization Processes
Inconsistencies during the lyophilization process directly impact image quality and, consequently, the accuracy of AVI. These inconsistencies result in variations in the appearance of the lyophilized cake, making defect detection more challenging.
- Uneven cake surfaces: Irregular surfaces scatter light, creating uneven illumination and obscuring potential defects.
- Cracks and fissures: These imperfections can be subtle and difficult to distinguish from variations in the cake's natural structure.
- Variations in fill level: Inconsistent fill levels lead to variations in lighting and shadowing, complicating image analysis.
- Presence of residual moisture: Residual moisture can cause glare and reflections, interfering with clear visualization of the lyophilized cake.
These variations significantly affect lighting, contrast, and overall image quality, making the detection of defects like particulate matter, cracks, or other imperfections difficult for even advanced automated systems. Careful control of the lyophilization process is crucial for minimizing these variations and improving image consistency.
Dealing with Glare and Reflections
The glass vials and the lyophilized cake itself can create significant glare and reflections, interfering with accurate image analysis. These reflections can mask defects, leading to false negatives and compromising the reliability of the inspection process.
- Strategies for controlling lighting: Utilizing diffused lighting, optimized lighting angles, and polarized light sources can minimize glare and improve image clarity.
- Anti-reflective coatings on vials: Applying anti-reflective coatings to the vials reduces surface reflections, improving image quality and reducing the need for complex image processing algorithms.
- Advanced image processing techniques: Sophisticated algorithms can be employed to identify and compensate for glare and reflections, improving the accuracy of defect detection.
Selecting appropriate lighting angles and intensities is crucial. Advanced algorithms, such as those based on polarization analysis or glare removal techniques, play a vital role in mitigating the impact of glare and reflections on automated visual inspection.
High-Throughput Requirements and Speed
Pharmaceutical manufacturing demands high-throughput inspection to maintain production efficiency. Balancing speed and accuracy is a critical challenge in automated visual inspection of lyophilized vials.
- High-speed camera systems: Implementing high-speed camera systems allows for faster inspection without compromising image resolution.
- Efficient image processing algorithms: Optimizing algorithms for speed and accuracy is essential for high-throughput inspection. Parallel processing techniques are often utilized to reduce processing time.
- Parallel processing techniques: Distributing the image processing workload across multiple processors allows for significantly faster processing, enabling higher throughput.
The trade-off between speed and accuracy must be carefully managed. The system must be optimized to achieve the required throughput while maintaining a high level of accuracy and minimizing false positives and false negatives.
Advanced Image Processing and Algorithm Development for Lyophilized Vials
Effective automated visual inspection of lyophilized vials depends heavily on sophisticated image processing and advanced algorithms. These algorithms must be capable of detecting subtle defects while minimizing errors.
Defect Detection Algorithms
Identifying defects in lyophilized vials requires specialized algorithms that can handle the complexities of the images.
- Machine learning: Machine learning models, trained on large datasets of images with and without defects, can learn to identify subtle variations indicative of defects.
- Deep learning: Deep learning algorithms, particularly convolutional neural networks (CNNs), excel at identifying complex patterns and features in images, improving the accuracy of defect detection.
- Computer vision techniques: Techniques such as edge detection, pattern recognition, and texture analysis are used to identify defects based on their visual characteristics.
The choice of algorithm depends on factors such as the types of defects being detected, the complexity of the images, and the available computational resources. The effectiveness of different algorithms in handling the complexities of lyophilized vial images is a key consideration.
False Positive and False Negative Reduction
Minimizing both false positives (rejecting good vials) and false negatives (accepting defective vials) is crucial for maintaining high quality standards.
- Data augmentation techniques: Increasing the size and diversity of the training dataset through data augmentation reduces the likelihood of overfitting and improves the robustness of the algorithms.
- Robust feature extraction: Developing robust features that are less sensitive to variations in lighting and other image artifacts improves the accuracy of defect classification.
- Algorithm optimization: Fine-tuning algorithms and hyperparameters through rigorous testing and validation improves their performance and reduces errors.
- Statistical process control (SPC) integration: Integrating SPC into the AVI process provides ongoing monitoring and control of the inspection process, enabling early detection of potential issues.
These strategies are essential for improving the overall reliability and accuracy of the automated visual inspection system.
Data Management and Analysis
The large datasets generated by AVI systems require robust data management and analysis capabilities.
- Data storage solutions: Cloud-based storage solutions or high-capacity on-site servers are needed to manage the vast amount of image data generated.
- Data analytics tools: Specialized data analytics tools are used to analyze the data, identify trends, and improve the performance of the algorithms.
- Process capability analysis: This statistical analysis technique assesses the capability of the AVI system to meet the required quality standards.
- Statistical process control (SPC): SPC charts help monitor the process and detect any deviations from expected performance.
Data analysis plays a crucial role in identifying trends, improving algorithm performance, and enhancing the overall quality control process.
Validation and Regulatory Compliance for Automated Visual Inspection Systems
Ensuring regulatory compliance is paramount for any pharmaceutical manufacturing process, including automated visual inspection.
Meeting Regulatory Requirements
Automated visual inspection systems used in pharmaceutical manufacturing must meet stringent regulatory requirements.
- 21 CFR Part 11 compliance: The system must comply with the FDA's 21 CFR Part 11 regulations for electronic records and signatures.
- Validation protocols: Thorough validation protocols are required to demonstrate that the system consistently meets its performance specifications. This includes Installation Qualification (IQ), Operational Qualification (OQ), and Performance Qualification (PQ).
Meeting these regulatory requirements is critical for ensuring the trustworthiness of the inspection results and maintaining compliance.
Performance Verification and Ongoing Monitoring
Continuous monitoring and verification are crucial for maintaining the accuracy and reliability of the AVI system over time.
- Regular performance checks: Regular checks using control samples and known defects are needed to confirm the system's continued accuracy.
- Calibration procedures: The system should be calibrated regularly to ensure accurate measurements.
- Ongoing training for operators: Operators require ongoing training to maintain their proficiency in using the system.
- Use of control samples: Incorporating control samples with known defects and no defects into the inspection process helps ensure accurate and reliable results.
These practices ensure continued compliance, minimize the risk of errors, and maintain high standards in lyophilized vial production.
Conclusion
Successfully implementing automated visual inspection of lyophilized vials requires addressing significant challenges in image acquisition, algorithm development, and regulatory compliance. By optimizing image acquisition techniques to minimize glare and reflections, developing sophisticated image processing algorithms to accurately detect subtle defects, and ensuring full regulatory compliance through rigorous validation and ongoing monitoring, pharmaceutical manufacturers can significantly improve the efficiency and reliability of their quality control processes. Investing in advanced automated visual inspection solutions is crucial for maintaining high standards in lyophilized vial production and ultimately improving patient safety. Consider exploring the latest advancements in automated visual inspection of lyophilized vials to enhance your quality control strategy and ensure the highest quality product for your patients.
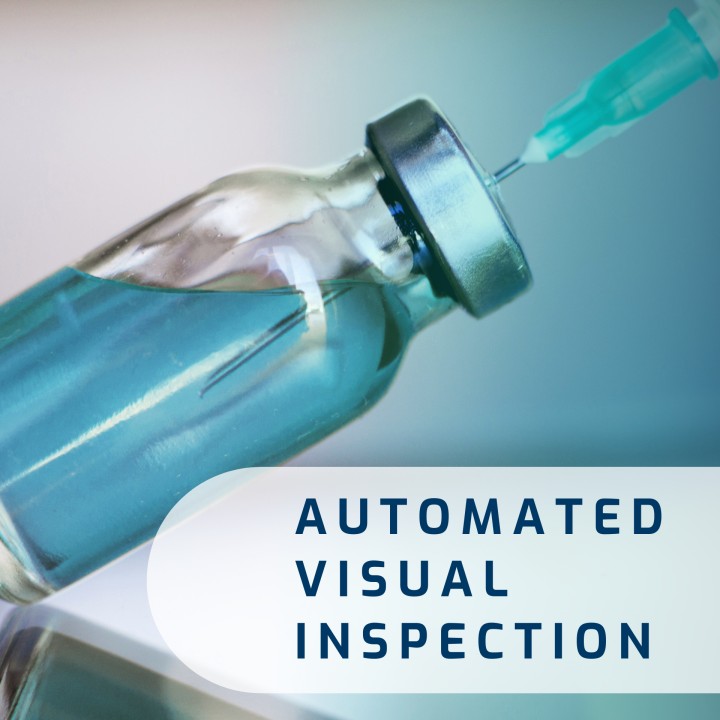
Featured Posts
-
Asylum Shelter Reform E1 Billion In Savings Possible Through Better Organization
May 11, 2025 -
Thomas Mueller Bayern Munich Analyse D Une Reponse Intelligente A Un Journaliste
May 11, 2025 -
Win Tickets For Tales From The Track Relay Presented
May 11, 2025 -
Sydney Mc Laughlin Levrones World Leading 400m Hurdle Run In Miami
May 11, 2025 -
Adam Sandlers Net Worth A Case Study In Comedic Success
May 11, 2025