The Future Of Automated Visual Inspection For Lyophilized Vials: Tackling Current Limitations
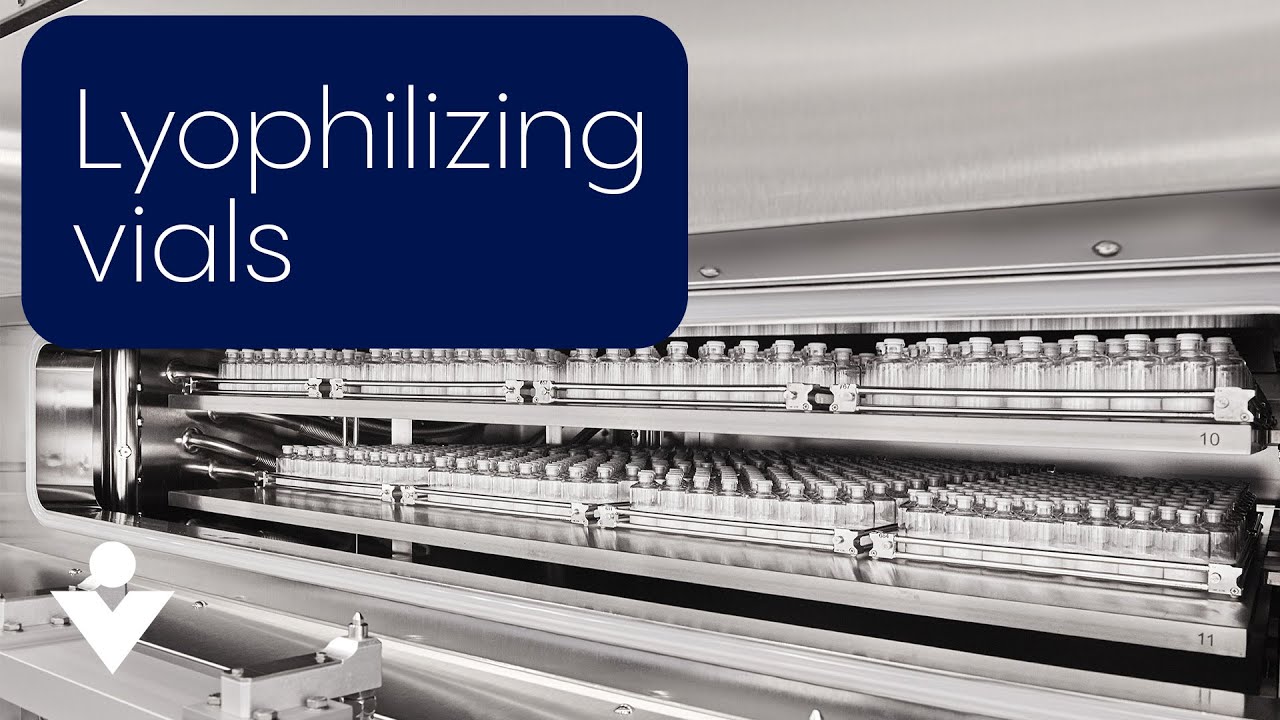
Table of Contents
Current Limitations of Automated Visual Inspection Systems for Lyophilized Vials
Several challenges currently restrict the full potential of automated visual inspection systems for lyophilized vials.
Challenges in Image Acquisition: Capturing clear, high-resolution images of lyophilized vials is surprisingly difficult. The curved surface of the vials, coupled with the often-present frost formation and variations in lighting, significantly complicates the process.
- Glare and Reflections: The glass surface can create significant glare and reflections, obscuring potential defects.
- Shadowing: Uneven lighting can cast shadows, masking critical details.
- Material Variations: Different vial materials (e.g., glass type, coatings) affect light reflection and image quality.
Overcoming these challenges requires advanced imaging techniques. Multispectral imaging, capable of capturing images across a range of wavelengths, and 3D imaging, providing a complete three-dimensional view of the vial, offer promising solutions.
Difficulty in Defect Detection and Classification: Differentiating between critical defects and innocuous variations is a significant hurdle. A lyophilized cake might exhibit minor variations in appearance due to the freeze-drying process itself, which shouldn't necessarily trigger rejection.
- Critical Defects: Particulate matter, cracks, delamination, and vial breakage are critical defects requiring immediate attention.
- AI and Machine Learning Limitations: Current AI and machine learning algorithms struggle to consistently distinguish critical defects from acceptable variations. The algorithms need extensive training data encompassing the diverse appearances of lyophilized products. The variability in lyophilization processes leads to inconsistencies in the appearance of acceptable products, challenging accurate algorithm training.
Robust training datasets, representing a wide range of vial types and lyophilization processes, are crucial for improving the accuracy and reliability of AI-based defect detection.
High Initial Investment and Implementation Costs: Implementing automated visual inspection systems involves substantial upfront costs.
- Hardware and Software Costs: The cost of high-resolution cameras, advanced imaging systems, powerful computing hardware, and sophisticated software is significant.
- Integration and Validation: Integrating the system into existing manufacturing lines and undergoing rigorous validation processes add further expense.
- Ongoing Maintenance: Regular maintenance and potential software upgrades also contribute to the overall cost.
Cost-saving strategies, like leasing equipment or adopting cloud-based solutions, could alleviate some of the financial burden.
Regulatory Compliance and Validation: Stringent regulatory requirements govern the use of automated inspection systems in pharmaceutical manufacturing.
- FDA 21 CFR Part 11 Compliance: Ensuring compliance with regulations like FDA 21 CFR Part 11 regarding electronic records and signatures is crucial.
- Validation Procedures: Thorough validation is required to demonstrate the accuracy, reliability, and repeatability of the automated system.
- Data Integrity: Maintaining data integrity and traceability throughout the inspection process is essential for regulatory compliance.
Technological Advancements Driving the Future of Automated Visual Inspection
Several technological advancements are poised to revolutionize automated visual inspection for lyophilized vials.
Artificial Intelligence and Machine Learning: AI and ML are central to improving the accuracy and efficiency of automated inspection.
- Deep Learning and CNNs: Deep learning techniques, particularly convolutional neural networks (CNNs), are exceptionally well-suited for image analysis and defect detection.
- Self-Learning Algorithms: Self-learning algorithms continuously refine their performance based on new data, adapting to variations in lyophilized products over time.
Advanced Imaging Techniques: Emerging imaging technologies offer enhanced defect detection capabilities.
- Hyperspectral Imaging: Captures images across a wide range of wavelengths, allowing for the detection of subtle defects invisible to conventional cameras.
- Terahertz Imaging: Provides high-resolution images through opaque materials, facilitating the detection of internal defects.
- 3D Imaging: Offers a complete 3D representation of the vial, enhancing defect detection and characterization.
Improved System Integration and Automation: Seamless integration of automated visual inspection systems with other manufacturing processes is key to optimizing overall efficiency.
- Robotics and Automation: Robotics and automation can streamline the handling and movement of vials, improving throughput.
- Data Analytics: Data analytics can provide insights into defect trends and help optimize manufacturing processes.
- Real-time Feedback: Real-time feedback from the automated inspection system can allow for immediate adjustments to the manufacturing process.
Conclusion:
Automated visual inspection for lyophilized vials faces challenges related to image acquisition, defect detection, cost, and regulatory compliance. However, advancements in AI, advanced imaging, and system integration are rapidly overcoming these limitations. The future of pharmaceutical manufacturing hinges on embracing these technological advancements. Embrace the future of pharmaceutical manufacturing by investing in advanced Automated Visual Inspection for Lyophilized Vials solutions today.
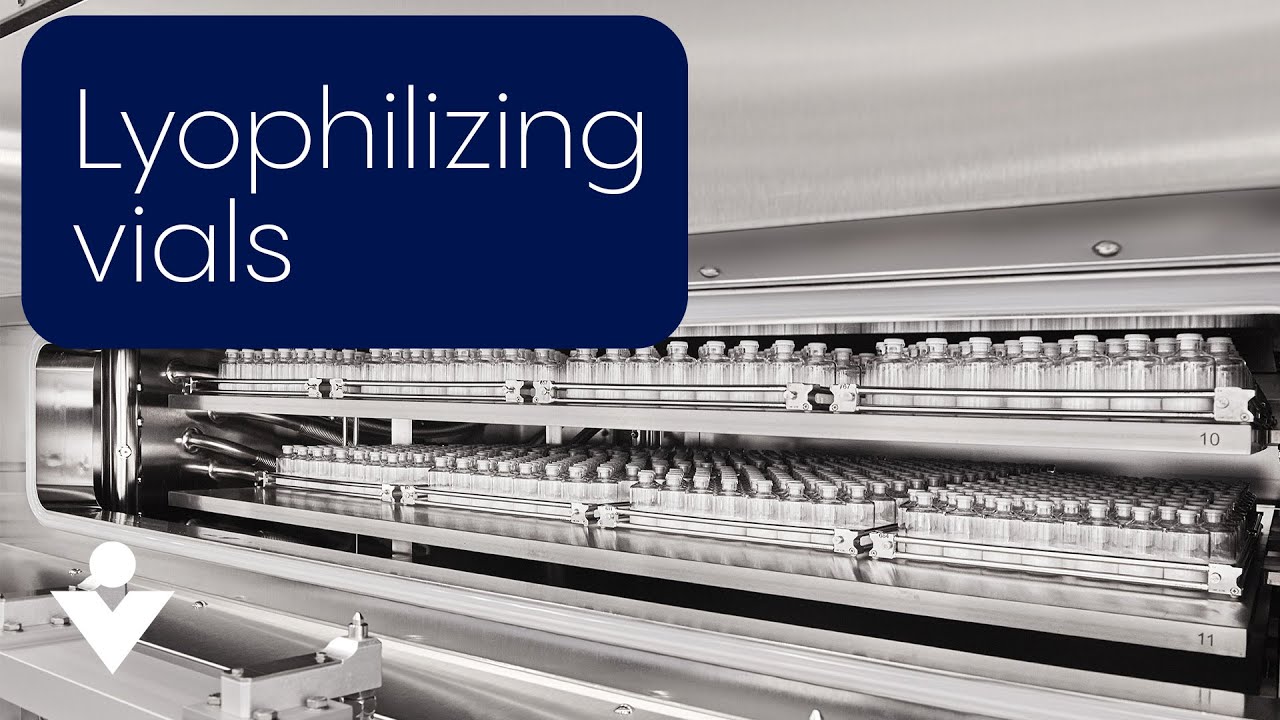
Featured Posts
-
Bellators Freire Ready For Showdown With Ufc Legend Jose Aldo
May 11, 2025 -
Reviving Downtowns The Role Of Sports Stadiums In Urban Renewal
May 11, 2025 -
Is Aaron Judge A Hall Of Famer His Performance After 1 000 Games
May 11, 2025 -
Magic Johnson Weighs In Who Wins The Knicks Pistons Series
May 11, 2025 -
The Challenge 41 Spoilers Shocking Elimination Of A Fan Favorite
May 11, 2025